In 2008, the Mosaic Corporation, the leading producer of potash and phosphate nutrients for agriculture, began an effort to improve the productivity of its Wingate phosphate mining operation in Florida. In the industry, rock recovery—the percentage of valuable material derived from ore—averages 85 to 90 percent. Wingate operated at just 47 percent rock recovery, a figure that raised concerns about the mine’s long-term viability. At the outset, managers expected minimal change. But armed with an excellent knowledge of process improvement and powerful tools including Minitab® Statistical Software, the Six Sigma team increased productivity by more than 50 percent and made a financial impact of more than $12 million per year. The team’s project also won a 2009 Process Excellence Award from the International Quality and Productivity Council.
The Challenge
The Wingate Mine had been owned by several companies over the years, but never performed to expectations. For that reason it was closed in 1999, and remained so until Mosaic acquired and restarted it in 2007. But the reopened mine’s low recovery rates couldn’t sustain continued operation long.
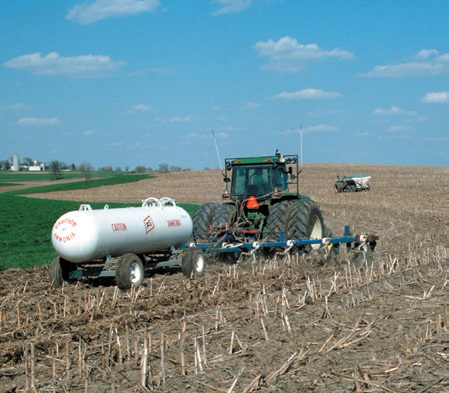
When the world's leading producer of phosphate crop nutrients set out to boost efficiency, the company trusted its critical data analysis to Minitab Statistical software.
Phosphorus is extracted from raw ore through a process called beneficiation. At Wingate, mined ore is slurried into a pit, then pumped to the beneficiation plant. There, pebbles, fine clays and sand are separated from the phosphate rock by washing and screening. The phosphate rock is then treated with reagents for further refining. Somewhere in this process, the mine was falling short. It fell to Six Sigma Black Belts Joe Gliksman and John Whitley to apply their knowledge of quality improvement methods to help the mine’s staff boost profitability, and they brought Minitab with them.
Mosaic has invested in Lean Six Sigma since the company was founded in 2004 by the merger of Cargill and International Minerals Corporation. In 2008 alone, its quality initiatives involved more than 45 teams, engaged over 500 employees and delivered close to $25 million to the company’s bottom line. But when the Wingate Mine team began their work, expectations were minimal. “Managers hoped for a 2 or 3 percent increase in recovery rates,” Gliksman recalls. “They told us that sustained 70 percent recoveries at this mine would be a miracle.”
How Minitab Helped
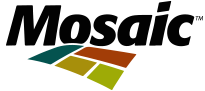
Organization
Mosaic Corporation
Overview
- World's leading producer of potash and phosphate crop nutrients
- Annual net sales exceeding $9.8 billion
- Employs approximately 7,400 people worldwide
Products Used
Minitab® Statistical Software
Results
- Increased recovery rates to over 80%
- Over 50% increase in concentrate phosphate rock production
- A financial impact of $12 million per year
- $8 million from increased production
- $4 million from decreased reagent needed per ton of rock processed