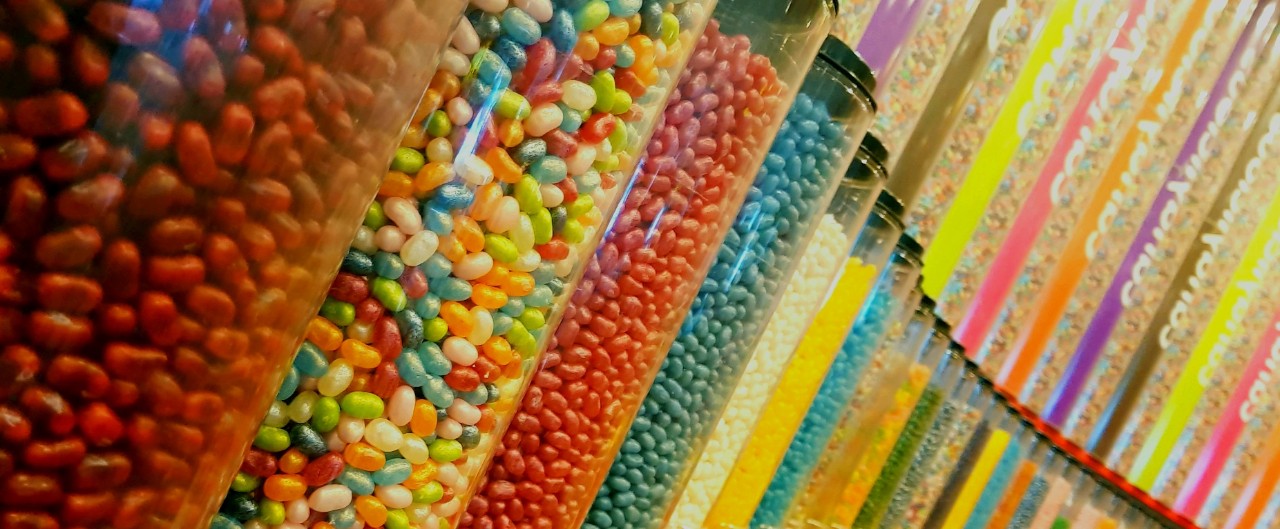
For over 50 years, USC Consulting Group (USCCG) has been driving operational excellence with a mission to provide real value by improving financial performance. USCCG helps companies reach their highest potential by improving processes and operations across their entire supply chain. Minitab’s solutions play an essential role in helping USCCG solve problems for their customers and remain a key component of enabling their operations to continue running at optimal levels.
The Challenge
If you are in the business of filling packages, you know the importance of controlling fill processes. Overfill has the same net effect as giving away money to your customers. In high volume operations, this can quickly add up to hundreds of thousands of dollars on an annual basis. On the other hand, if you under-fill, the fines and the damage to your reputation can be even more costly.
When filling packages, the first requirement is to meet governmental regulations for compliance with net content declarations on packaged goods. Simply put, your unit fill weights must be above a specified minimum, according to the Maximum Allowable Variance (MAV). Your average fill weight must be at or above, never below, the label declaration.
Many companies today feel that overfilling is the only way to avoid regulatory fines and maintain customer loyalty. Thus, their goal is to get as close as possible to the declared package weight without going under it. This seems perfectly sensible, but many companies have difficulties meeting this goal. Is it because they do not fully understand their process capabilities? Or have they not adopted correct tools and techniques, e.g., Lean, Six Sigma, or technology, to help reduce variation and control processes? Perhaps it is simply a matter of execution. The answer lies in part or all the above.
Minimizing and controlling fill weight variation and performing statistical modeling can redirect a considerable amount of money to your bottom line. Minitab is the solution of choice to optimize fill weight and has helped customers across a variety of industries reduce millions of dollars of overfill.
How Minitab Helped
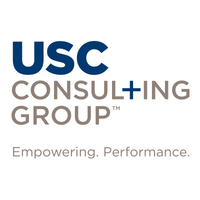
The Organization
- Operations management consulting firm with specialty in process improvement
- Headquartered in Tampa, FL
- Employs around 200 people
The Challenge
When filling packages, the first requirement is to meet governmental regulations for compliance with net content declarations on packaged goods. Unit fill weights must be above a specified minimum, while the average fill weight must be at or above, never below, the label declaration.
Products Used
Minitab® Statistical Software
Results
- Overfill for packaged candy was reduced by more than 50%.
- More than $1.2 million of annual material savings.