OneSteel fabrica y distribuye más de 40,000 productos a aproximadamente 30,000 clientes de las industrias de construcción, manufactura, viviendas, minería y agricultura. En instalaciones de toda Australia, la compañía fabrica productos que van de vigas gruesas a alambres de acero delgados. OneSteel descubrió que una de sus instalaciones producía barras con una variación considerable en la cantidad de “sarro”, óxido de hierro que se forma cuando la superficie de acero caliente reacciona con el oxígeno del aire durante el procesamiento. Es necesario retirar el sarro antes de continuar con el procesamiento para evitar el desgaste de equipos costosos y defectos en el producto final. La formación de una pequeña cantidad de sarro es inevitable, pero el exceso de sarro puede causar una pérdida significativa del rendimiento. OneSteel designó a un equipo para reducir el sarro en las barras a un nivel aceptable. Los miembros del equipo utilizaron el Minitab Statistical Software para analizar sus datos y demostrar el éxito de su proyecto.
Reto
El metal bruto de OneSteel pasa de una instalación a otra durante el proceso de refinación y procesamiento hasta llegar al producto final. Para producir una hebra de alambre, la planta Laverton Rod Mill de la compañía convierte el acero bruto caliente en una barra delgada, que luego pasa por un nuevo procesamiento. En Geelong Wire Mill, estas barras son calentadas a una temperatura mucho más baja y luego estiradas en frío a través de troqueles para producir hebras de alambre con diámetros y propiedades mecánicas específicas.
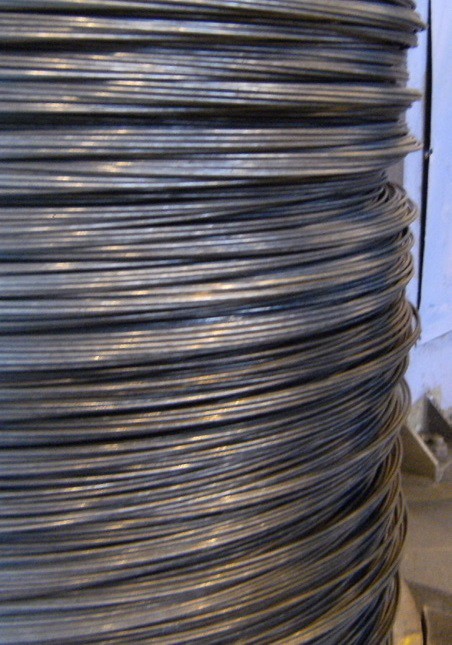
Cuando la cantidad de “sarro de planta” en una barra de acero de la planta Laverton Rod Mill de OneSteel comenzó a afectar el rendimiento y la rentabilidad en la planta Geelong de la compañía, ésta utilizó Six Sigma y el poder del Minitab Statistical Software para encontrar soluciones—y demostrar su éxito.
Para producir una barra en Laverton, el acero es calentado a una temperatura de por lo menos 1038° C y laminado. Posteriormente, la barra pasa por cajas de agua, donde es enfriada mediante una aplicación superficial de agua mientras pasa por la planta. Posteriormente, la barra es enviada a un cabezal de alineación, donde se corta de acuerdo con un patrón de anillos. Estos anillos se colocan sobre una cinta transportadora, donde se enfrían aún más y se acumulan en espirales.
El procesamiento a altas temperaturas en la molienda forma óxidos de hierro, llamados “sarro de planta”, sobre la superficie de la barra. Los niveles de sarro varían de acuerdo con el tipo de molienda utilizada, la temperatura del acero y el tiempo que éste permanece caliente. La naturaleza abrasiva de las partículas de polvo provenientes del sarro reduce considerablemente la vida útil de la hilera de trefilado y produce un producto de calidad inferior. Por lo tanto, para producir exitosamente alambres de acero a partir de la barra, es necesario remover primero el sarro. Geelong Wire Mill utiliza un proceso mecánico llamado decapado de doblado inverso, según el cual las barras pasan por una serie de haces. El doblado hace que el óxido de sarro se suelte sin causar daños al acero flexible, pero el nivel de sarro en las barras de Laverton a menudo estaba por encima del nivel deseado para un decapado mecánico y el resultado era un menor rendimiento. Los costos adicionales de exceso de sarro incluyen el gasto de limpieza y desecho de éste, los costos asociados con el funcionamiento y mantenimiento del sistema de extracción de sarro y los costos potenciales de tasas de corridas más bajas, vida útil más corta de las hileras, mayor consumo de lubricante y menor calidad del producto. Considerando que en 2008 la instalación Geelong Wire Mill gastó $815,000 para mantenimiento, lubricante e hileras, la reducción del sarro en las barras entrantes podía generar un ahorro significativo para OneSteel.
Cómo ayudó Minitab
Brett Perrin, Six Sigma Black Belt, y el propietario del proceso Shanti Arangala, con el apoyo de su campeón, Brian O’Connell, comenzaron su proyecto en agosto de 2008. Su equipo incluía a miembros de ambas instalaciones, incluyendo gerentes técnicos, ingenieros de procesos, profesionales de control de calidad, un metalúrgico y operadores de equipos.
Mediante la metodología DMAIC (sigla en inglés para Definir, Medir, Analizar, Mejorar y Controlar), el equipo del proyecto estudió el proceso de fabricación de alambres y definió una barra defectuosa como una barra con capacidad de decapado inferior a 95%. Posteriormente, tomó una muestra de las barras que llegaban a la planta Geelong Wire Mill provenientes de Laverton.
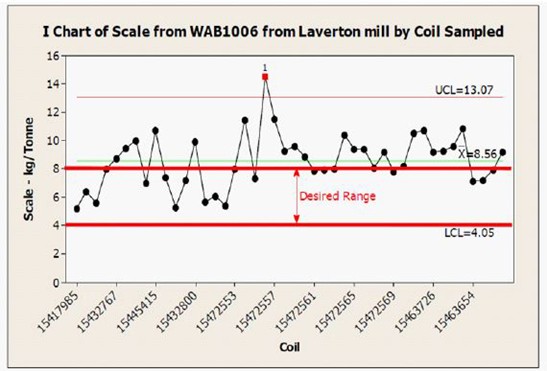
Cuando el equipo de proyectos de OneSteel midió el sarro sobre las barras de la planta de Laverton y analizó sus datos en Minitab, descubrió que 62% de las muestras probadas tenían niveles de sarro inaceptablemente altos.
El equipo midió el peso del sarro como una proporción del producto total (bobinas de barras de acero) en Kg./tonelada. Descubrió que 62% de las muestras bajo prueba era superior a 7 Kgs. por tonelada, con una variación significativa de hasta 3 Kgs. por tonelada. Esto genera una pérdida significativa del rendimiento, porque una variación de apenas 1 Kg. por tonelada equivale a $75,000 en rendimiento. En la planta Geelong, la pérdida a causa del exceso de sarro se estimó en aproximadamente $220,000 por año.
A lo largo del proyecto, los miembros del equipo acudieron a Minitab para analizar sus datos y comunicar la importancia de sus resultados. Por ejemplo, utilizaron la prueba t de 2 muestras de Minitab para probar la diferencia en el peso del sarro según la graduación de las barras de acero, pero también utilizaron una gráfica de cajas para mostrar visualmente la información.
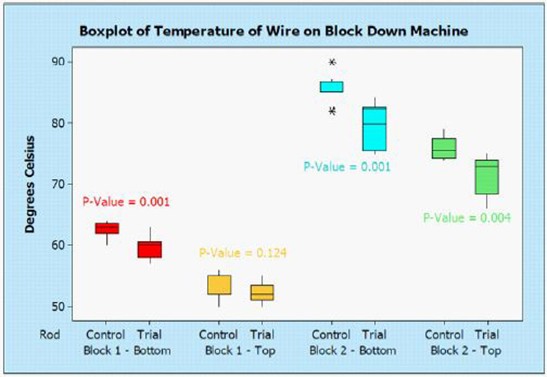
Una gráfica de cajas de los datos de temperatura de la maquinaria recolectados bajo condiciones de control y prueba muestra las temperaturas más bajas obtenidas en las corridas de prueba.
Utilizaron el análisis de regresión de Minitab para revelar la relación entre la temperatura del cabezal de alineación y el peso del sarro, y utilizaron la gráfica de dispersión del software para mostrar visualmente esta relación.
El equipo también aplicó la función de densidad de probabilidad de Minitab a datos de muestreo reales y los comparó con un resultado deseado para determinar el ahorro potencial que podría acumularse como resultado de una menor variación y un peso más bajo del sarro.
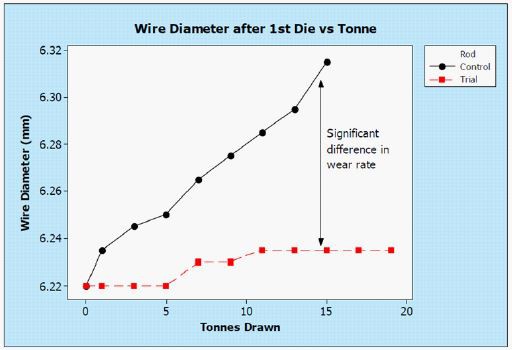
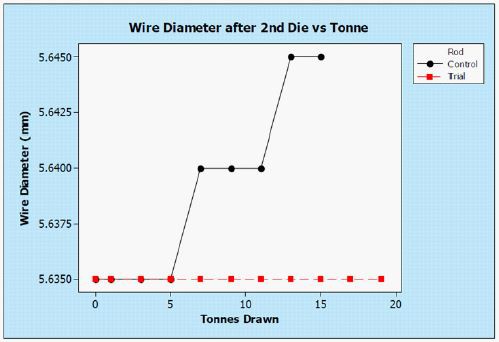
Las poderosas gráficas de Minitab permitieron que todos en el proyecto vean la diferencia en el desgaste de troqueles entre la corrida de prueba (roja) y la corrida de control (negra).
El análisis de Pareto determinó las calidades de las barras que causaban retrasos en las máquinas de trefilado. “Minitab no sólo hace esto rápidamente con una manipulación limitada de datos, sino que también tiene gráficas muy claras que son una herramienta de comunicación efectiva en las presentaciones”, indica Perrin.
Cambiar las características del material utilizado para crear las barras de acero en la planta Laverton Rod Mill no era una opción, así que el equipo buscó otras maneras de reducir el porcentaje de sarro de las barras e incrementar el rendimiento de la planta. Realizaron experimentos para probar los factores, incluyendo los procesos de enfriamiento utilizados en Laverton, las prácticas de decapado y trefilado utilizadas en la Geelong y los parámetros operativos en ambas plantas.
En primer lugar, realizaron una prueba para evaluar los efectos de los parámetros de la cinta de enfriamiento sobre la cantidad de sarro en una barra. Igualmente midieron las temperaturas del bloque de trefilado y del cabezal de alineación en Laverton. El análisis de Minitab reveló una diferencia significativa cuando la temperatura de reforma sobre la cinta de enfriamiento se redujo en 30%.
Posteriormente, probaron los efectos de los métodos de trefilado sobre el rendimiento. Para la corrida de controles y la corrida de pruebas, el equipo estableció líneas de producción con nuevos troqueles, nuevo lubricante para cada troquel, nuevos cepillos en la unidad de decapado y velocidad constante de las corridas. La corrida que utilizaba sus parámetros de prueba generó temperaturas más bajas, un producto más limpio, un desgaste menor del troquel y menos sarro visible. Una prueba de resistencia no mostró diferencia estadística entre la calidad del producto de prueba y el producto de control.
Midieron el desgaste del troquel en la máquina de trefilado y descubrieron que los nuevos parámetros también afectaron significativamente la vida útil de los troqueles. En una prueba, el diámetro del alambre proveniente de un troquel era de 6.22 mm al inicio de la corrida. Luego de pasar 15 toneladas de alambre utilizando la barra de control, el troquel había alcanzado un diámetro de casi 6.32 mm. El desgaste del troquel para la línea que utilizaba la barra de prueba fue significativamente inferior—después de 15 toneladas, el diámetro era inferior a 6.24 mm.
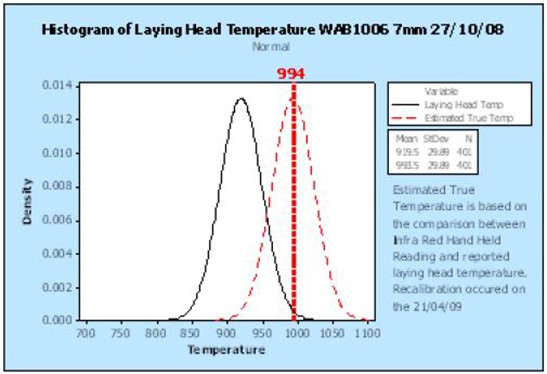
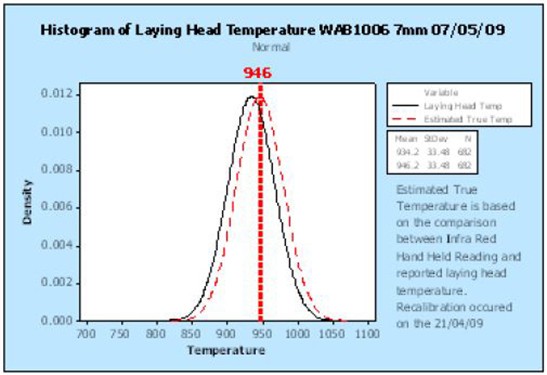
El análisis de datos recolectados antes y después revela el impacto de las mejoras al procedimiento de calibración para el cabezal de alineación en la planta Laverton Rod Mill. Los cálculos “verdaderos” y más precisos de temperatura permiten que la planta asegure que los niveles de sarro en sus barras estén dentro de los límites aceptables.
Luego de implementar varias mejoras, el equipo utilizó Minitab para analizar el peso del sarro y la temperatura del cabezal de alineación para un laminado de alambre de 7 mm. El análisis de Minitab confirmó que Laverton puede producir barras apropiadas para decapado mecánico con una pérdida de rendimiento debido al sarro mucho más baja que en el pasado.
Mediante Minitab, el equipo creó gráficas de control que claramente mostraban el efecto de las pruebas realizadas en la planta. Fue una manera efectiva de comunicar el resultado de las pruebas a los propietarios del proceso.
Resultados
Los esfuerzos del equipo han mejorado el proceso de enfriamiento en la planta Laverton Rod Mill. Los operadores ahora tienen mejor control de la temperatura del cabezal de alineación, y el análisis de Minitab ha confirmado que el proceso de enfriamiento mejorado ha reducido significativamente el peso del sarro en la barra.
Los histogramas de Minitab que se encuentran a la derecha muestran cómo una mejora en el procedimiento de calibración de Laverton ha acercado la “verdadera” temperatura estimada y la registrada por el cabezal de alineación. Esto ha generado una reducción en las temperaturas reales del cabezal de alineación en comparación con laminados anteriores, y esta temperatura más baja es el principal causante de la reducción de pérdida de rendimiento en la forma de sarro de planta para los clientes de barras de acero.
La nueva barra de Laverton es un producto visiblemente superior y mucho más limpio para la planta Geelong Wire Mill. Como resultado de una menor cantidad de sarro y un mayor rendimiento, OneSteel anticipa un ahorro aproximado de $235,000 por año y de otros $40,000 en mano de obra e insumos. La reducción en el sarro también tiene beneficios adicionales de procesamiento.
Luego de confirmar las mejoras, el equipo de OneSteel ingresó en la fase de control de su proceso DMAIC. Utilizan las gráficas de control de Minitab para encerrar los cambios que han hecho a los procedimientos y actividades de mantenimiento, permitiendo mantener esta mejora y asegurar que los ahorros continúen en el futuro. Entretanto, la oficina Six Sigma de OneSteel ha encontrado nuevas maneras para aplicar el poder de la mejora de la calidad—y el Minitab Statistical Software—para mejorar la eficiencia y rentabilidad en cada rincón de sus operaciones mundiales.

ORGANIZACIÓN
OneSteel
REVISIÓN GENERAL
- Fabricante y distribuidor mundial de acero y productos de acero terminados
- Con sede en Australia
- Ingresos de 7,400 millones de dólares australianos
- Más de 11,500 empleados en todo el mundo
RETO
Disminuir el “sarro de planta” sobre las barras de acero utilizadas para producir alambre.
PRODUCTOS UTILIZADOS
Minitab® Statistical Software
RESULTADOS
- Ahorro de más de $275,000 por año
- Menos desgaste de la maquinaria
- Producto visiblemente superior